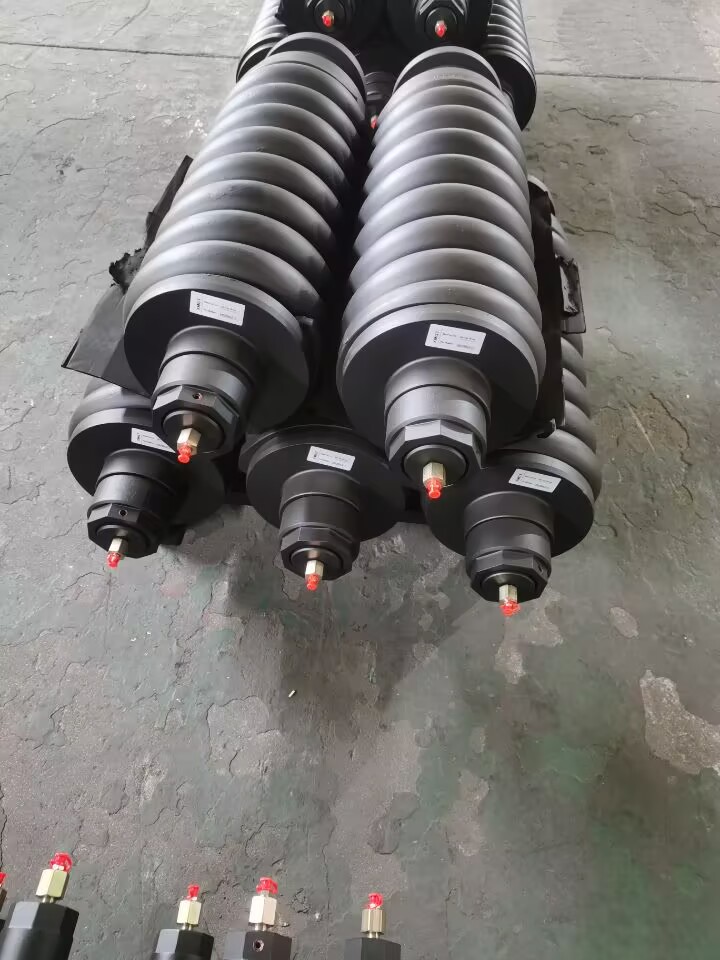
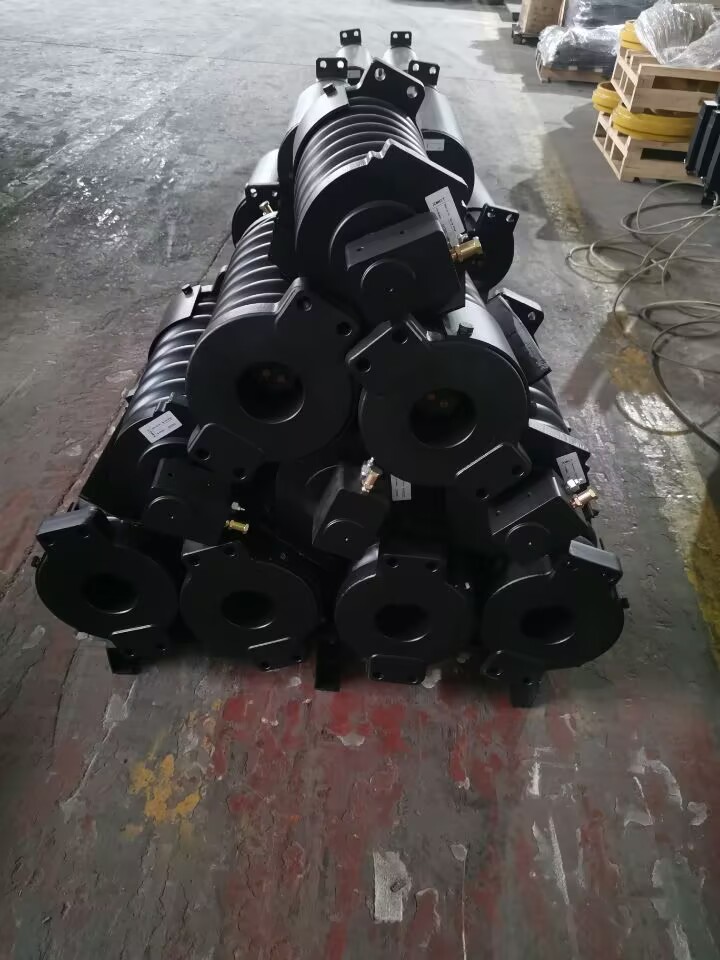
As a critical core component of construction machinery, OEMquality Track adjuster assemblies are essential for performance, reliability, and longevity.
Below are the key differences between standard and OEM-quality components and the reasons for prioritizing OEM quality:
I. Core Differences Between OEM and Standard Quality
1. Materials and Manufacturing Processes
OEM Quality: Utilizes high strength alloy steel and precision machining.
For example,hydraulic cylinder buffer systems achieve stable performance through precise alignment of buffer sleeves and inner bores. Materials are wear-resistant, corrosion-resistant, and comply with OEM design standards.
Standard Quality: May use lower grade steel or inferior materials with insufficient machining precision,leading to premature wear, oil leaks, or deformation—especially under high-pressure, high-frequency operating conditions.
2. Technical Specifications and Compatibility
OEM Quality: Strictly matches host machine requirements. Parameters such as spring installation length and load capacity are optimized for specific equipment models to ensure seamless integration.
Standard Quality: May have dimensional deviations or mismatched parameters, causing abnormal chain tension and operational instability, potentially leading to mechanical failures.
3. Lifespan and Reliability
OEM Quality: Rigorously tested for durability, with lifespans reaching tens of thousands of hours and low failure rates. For example, Sany Heavy Industry’s hydraulic cylinders outperform standard products and support the world’s largest-tonnage cranes
Standard Quality: Due to inferior materials and processes, lifespan may be 1/3 to 1/2 of OEM parts, with frequent failures like corrosion and oil leaks, particularly in harsh environments.
4. After-Sales Support and Warranty
OEM Quality: Includes comprehensive warranties from manufacturers or authorized channels (e.g., 4S service centers), with traceable part origins.
Standard Quality: Non-OEM parts may have shorter warranties and ambiguous liability terms, leaving users to bear repair costs if issues arise.
II. Why OEM Quality Is Necessary
1. Ensuring Safety and Efficiency Track adjuster failures can cause chain detachment or track misalignment. OEM parts minimize downtime risks, especially in extreme environments like mines or deserts.
2. Reducing Total Ownership Costs
While OEM parts have higher upfront costs, their extended lifespan and lower failure rates reduce long-term replacement and repair expenses. Standard parts may incur higher total costs due to recurring issues.
3. Maintaining Machine Performance
OEM components ensure system compatibility
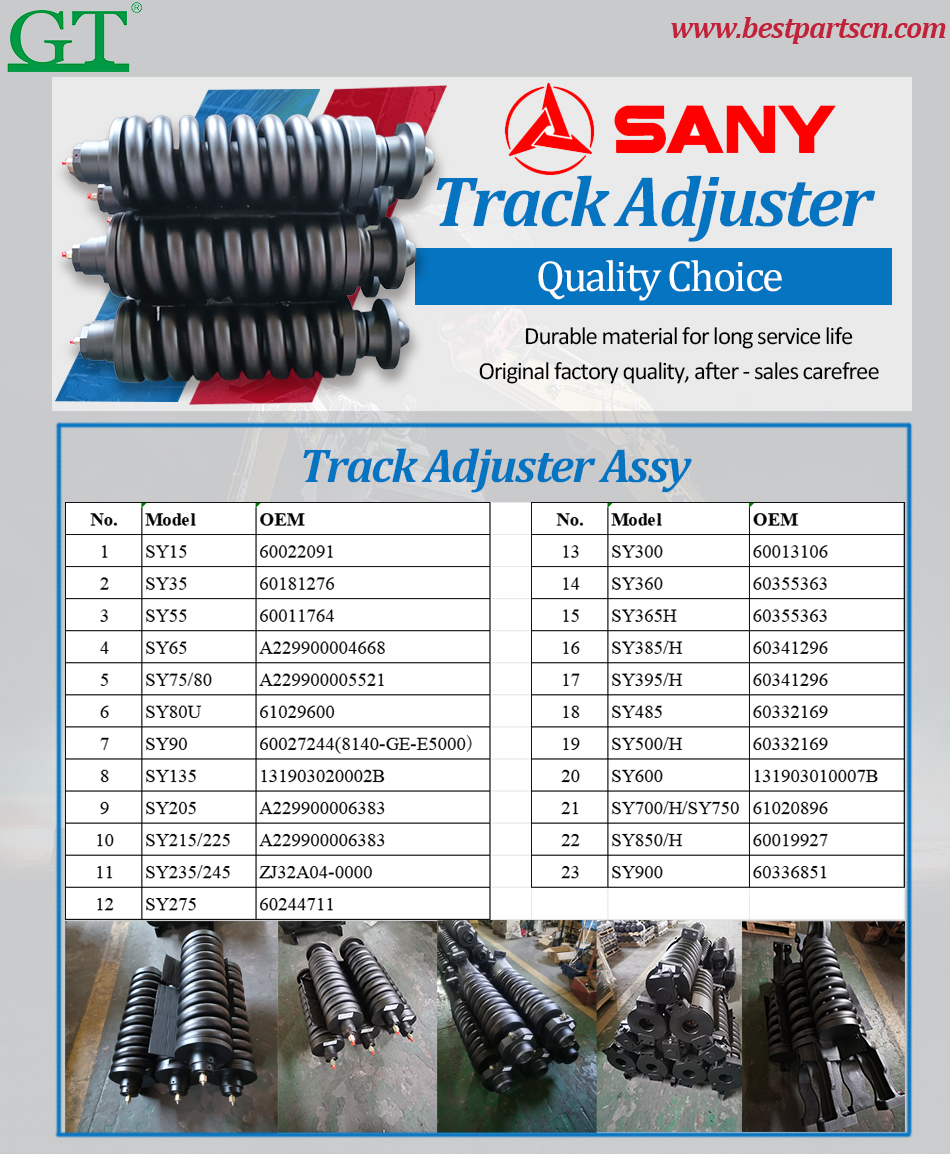
Post time: Apr-28-2025